In the past few years, the costs of housebuilding in the UK have soared above their pre-pandemic levels. The Government's Building Materials and Components Statistics analysis (June 2023) found that the cost of materials in new housing had increased by 7.6% in the year to April 2023. Included in this, the greatest individual increases were in Screws (33.7%), Insulating materials - thermal or acoustic (28.4%) and Ready-mixed concrete (24.5%). Conversely, the price of some materials saw large decreases (including concrete rebar, imported wood and fabricated structural steel). Construction Enquirer reports that annual House Building cost inflation in 2022 was 12.8%.
With such large increases in the cost of raw materials, inflationary pressures pushing labour costs higher, and increasing interest rates, it's more important than ever to get design, specification, procurement and workmanship done right first time, thereby avoiding costly remedial works. In this article, we will look at some of the cost-related isses that housebuilders face to do with acoustics, and how they can improve their chances for success first time.
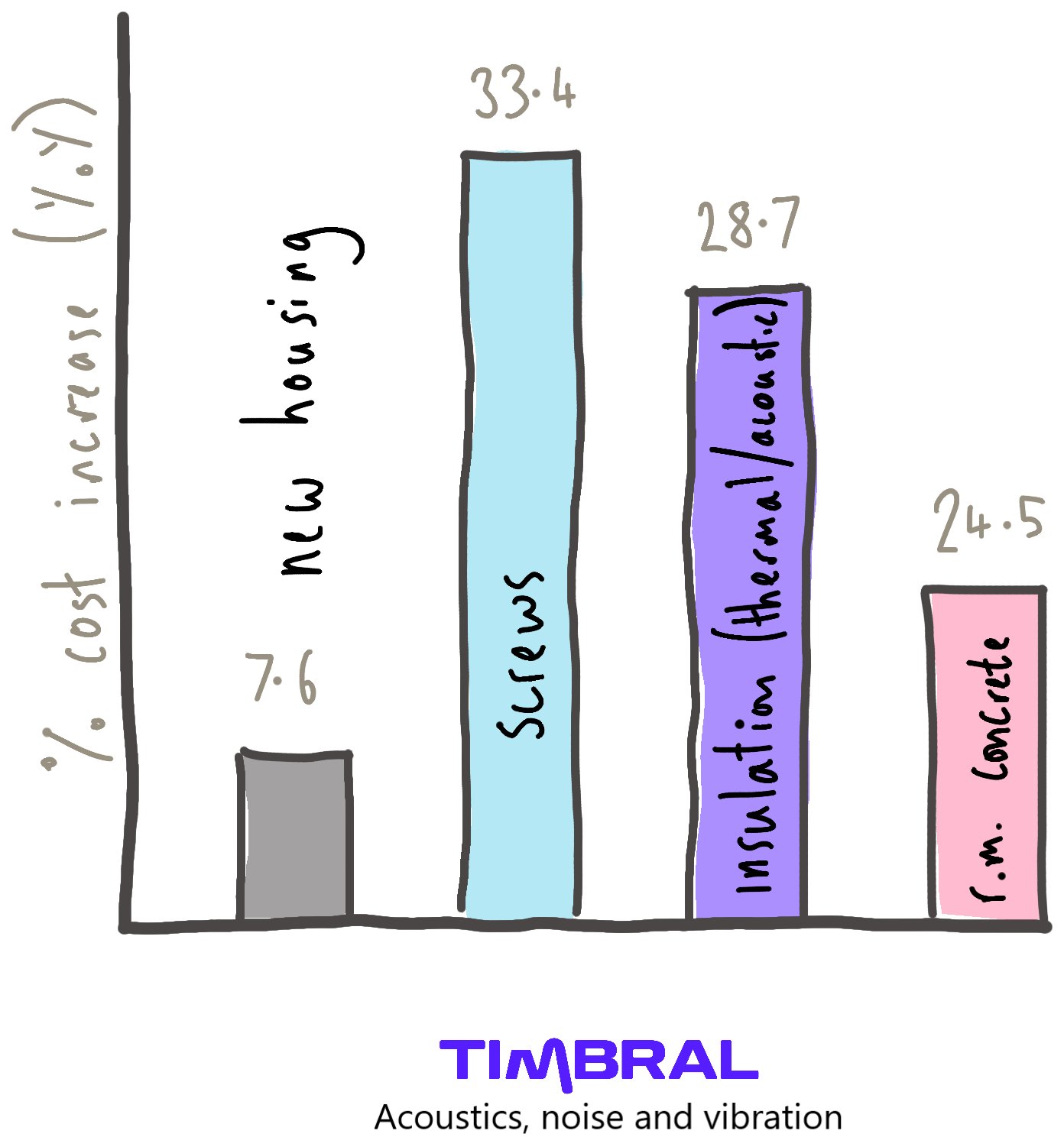
Influences on costs of structure, fit-out and finishes
The biggest impact on cost of structure from acoustics is likely to be one of two things:
- A requirement for a high level of sound insulation, or;
- Building isolation
A high level of sound insulation is usually required between commercial and residential demises. While Part E of the Building Regulations specifies minimum requirements for separation between demises, it does say that, "a higher standard of sound insulation may be required between spaces used for normal domestic purposes and communal or non-domestic purposes." In our experience, it is certainly worth providing an enhancement over and above the Building Regulations between commercial and residential areas, and this is often a requirement of planning conditions. Sound insulation across demises is usually dependent on a combination of structure and finishes.
Examples of the acoustical impacts on structure, fit-out and finishes could be:
- Increased thickness and density of concrete or drylining.
- Increased cavity sizes and reduces NIA.
- Detailing of junctions, floor finishes and penetrations.
Residential developments close to rail lines (above or overground), might need building isolation to mitigate groundborne noise and vibration. Building isolation generally consists of rubber bearings located on top of pile caps. The design and co-ordination of building isolation can be complex, and if not considered at an early stage, could result in large, unexpected costs due to changes in design and construction. If incorporated too late in the design, building isolation can also lead to compromises on quality and net internal areas (NIA), thereby reducing the potential gross development value (GDV).
Impact on costs of facades, ventilation and cooling
Facades and glazing are often considered one of the most expensive elements of a building, and they typically incorporate thermal and acoustic requirements. The acoustic requirement is usually dictated by external environmental noise - the most common sources being road, rail and air traffic. Other examples of anthropogenic sources of noise include commercial, industrial and entertainment noise.
Historically, internal noise levels from external sources were usually conditioned by Local Planning Authorities. This changed with coming into force of Part O of the Building Regulations in June 2022, which now requires maximum noise levels at night during the hottest days of the year. There is some overlap and between these two requirements, and you can find out more in our blog Acoustics vs Overheating.
In short, external noise can influence minimum glass thicknesses and cavity sizes, as well as the ventilation and cooling strategies. The noisier the environment, the higher the cost of the facade.
Is your residential development directly under a flight path, or adjacent to a motorway? If so, you can bet that facade and glazing specifications will need to be given due consideration, as well as the thermal and ventilation designs. All of these are issues which can be costly if dealt with by re-design at a late stage in the project.
If you're designing a concept for a residential development close to a major noise source, consider whether the following could help.
- Locate the houses as far from the noise/vibration sources as possible.
- Place common areas or non-habitable rooms on the noisiest facade.
- Use building massing and landscaping to screen sensitive facades and outdoor amenity areas from the source of noise.
- Consider innovate window designs (e.g. plenum windows).
How acoustics can impact the bottom line for housebuilders
We've seen some of the main considerations that should be given to acoustics, but what happens if these aren't considered appropriately at an early enough stage? There are generally three stages where the issue might be discovered.
Noise problems discovered at the detailed design stage can often be dealt with appropriately and designed out before construction begins. This often occurs in projects which had no acoustic consultant involved in the Stage 3 Design, and no consideration of noise was given by the Local Authority during the application. In the rare instance that a fundamental change to the building is required (e.g. if the facade requires major external changes), then the project may have to go back to planning, or the structural design may need revisiting.
When noise problems are discovered at the construction stage, they can again often be designed out, but the added cost of programme delays and wasted materials will eat away at housebuilders' profit margins. A typical example of this would be co-ordination of services in a ceiling void, where it is discovered that there is not enough space to incorporate attenuators or anti-vibration mounts.
Often, noise problems are only discovered during commissioning. If these result in a failure of pre-completion sound insulation testing, then the remedial works are usually considerable and can have a significant impact on the quality of the development, net internal areas and net profit. High building services noise levels from duct terminations or fan coil units can sometimes be reduced by minor adjustments to flow, or cleaning out filters. More fundamental issues to do with plant room noise and vibration can involve costly measures, such as retrospectively isolating plant, or providing additional linings to the plant room.
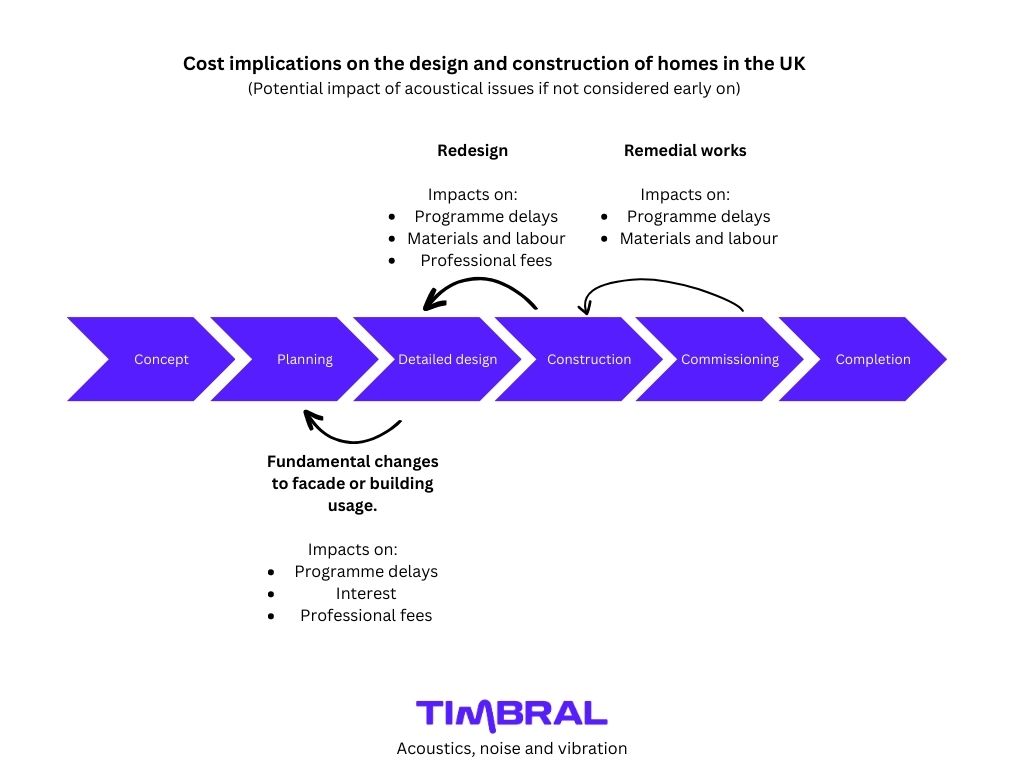
Protecting the bottom line
We have seen that there are several fundamental issues related to acoustics, noise and vibration, which can impact the bottom line for housebuilders. Some of these are related to Building Regulations, some are related to Planning, and some are simply best practice, to minimise risk of complaint and potential lawsuits that could follow.
The later the problem is realised, the bigger the potential impact on net profit and quality of the development. Each step backwards incurs additional costs in the form of programme delays, interest on loans, material and labour costs, professional and design fees.
The best way for housebuilders to protect their bottom line is to engage an experienced acoustic consultant in the early stages of the project.
A good acoustician will foresee potential issues and raise them early, to allow them to be designed out, thereby avoiding the costliest impacts at construction stage.
Contact us now to discuss your project, and see how we can help avoid unexpected costs.